Abuse-Resistant Gypsum Panels: Multi-Family Homes
Extra strength and toughness to reduce surface damage in high-traffic areas
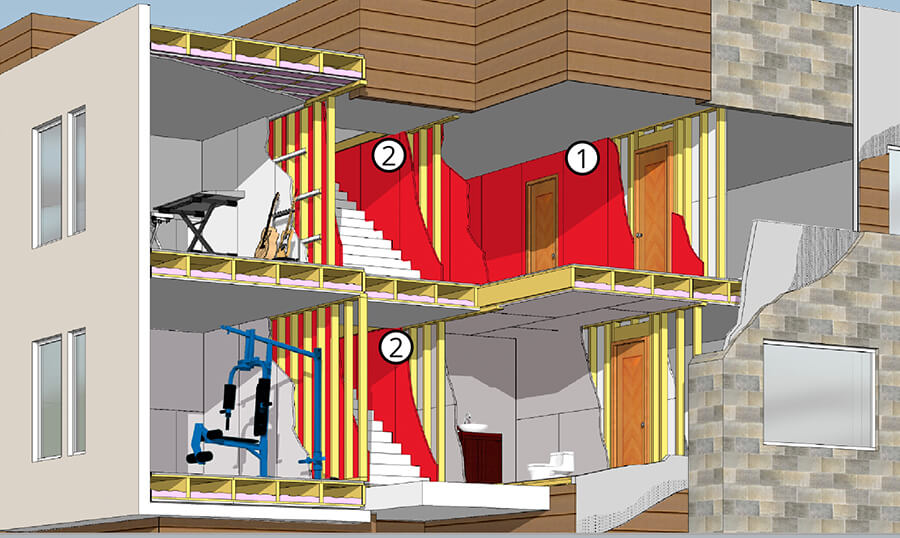
Abuse-Resistant Gypsum Panels improve wall protection against surface scuffs, abrasions and indentations.
Physical Description
Abuse-Resistant Gypsum Panels feature extra-tough front and back facers made of either heavyweight, reinforced-paper or durable fiberglass mats. Each panel’s core is engineered to provide a high-density, mold- and moisture-resistant, Type X gypsum board backbone. Long edges are typically wrapped with the facer material and tapered to simplify joint finishing while short edges are cut square. Abuse-Resistant Gypsum Panels are commonly manufactured in a 5/8” (15.9 mm) thickness, a 48” (1220 mm) width and lengths from 8’ (2440 mm) to 12’ (3660 mm). Paper-faced panels are increasingly produced with facers containing high percentages of recycled fiber and core formulations containing recycled gypsum content are becoming more common as well. The applicable product manufacturing standard is ASTM C1629.
Advantages and Benefits
Because protecting the appearance of a property while minimizing installation and maintenance costs are multi-family design priorities, a product like Abuse-Resistant Gypsum Panels can offer multiple project advantages during initial construction and beyond.
o Construction Efficiency – Thanks to a faster, easier and less-costly installation process, building damage-prone interior walls with Abuse-Resistant Gypsum Panels rather than alternatives like masonry-based systems or engineered architectural panels can help reduce material and labor costs as well as trim days off a project’s construction schedule. In addition, repair and remodeling of walls and partitions at a future date is much easier and more practical with Abuse-Resistant Gypsum Panels.
o Wall Performance – Abuse-Resistant Gypsum Panels are designed to stand up to the typical knocks, scrapes and scratches walls have to endure in areas where high traffic and busy activity increase the risk of damage. Their performance has been laboratory tested against surface wear and abrasions, minor indentations and both soft- and hard-body impacts.
o Maintenance Simplicity – Occasional repairs to minor surface damage and dents can be accomplished quickly, cost efficiently and effectively with common tools and techniques as well as basic carpentry skills.
o Mold and Moisture Protection – Abuse-Resistant Gypsum Panels not only help protect wall surfaces from damage but the underlying structures beneath them too. With enhanced resistance to moisture absorption, infiltration and mold growth, the entire wall assembly is better able to provide insulation, sound control and/or fire protection uncompromised by damage or decay.
o Fire Resistance – Abuse-Resistant Gypsum Panels can also contribute significantly to a multi-family residential structure’s fire protection strategy. They are produced with a non-combustible Type X core and are UL-classified for use in any fire-rated assembly where a 5/8” Type X panel is approved. Refer to GA-600 Fire Resistance and Sound Control Design Manual. Consult with gypsum manufacturer for specific recommendations.
o Noise Reduction – Reducing noise transmission is a very important objective in multi-family construction. As a key element in a long list of sound control assemblies anywhere 5/8” gypsum wallboard panels are specified, Abuse-Resistant Gypsum Panels can help block or reduce the intensity of unwanted noise transferred between rooms and between floors. Refer to GA-600 Fire Resistance and Sound Control Design Manual. Consult with gypsum manufacturer for specific recommendations. more
o Finishing Flexibility – Abuse-Resistant Gypsum Panels can be textured, painted or decorated with the same finishing flexibility as traditional drywall panels.
Damage-Resistance Classifications
To provide a way of comparing the expected performance of different brands of Abuse-Resistant Gypsum Panels, laboratory tests are conducted in accordance to ASTM C1629 to simulate wear that could be experienced in a multi-family application. Product samples are exposed to four different potentially damaging forces on specially designed test equipment and ranked into one of three different classifications based on the degree of damage each sample sustains.
o Surface Abrasion – Measures the ability of a gypsum panel’s facer to resist surface scratches and scuffs by exposing the panel to a 25 lb. weighted wire brush held against the sample’s surface while the sample is moved back and forth 50 times. Based on the depth of the abrasion at the conclusion of the test cycle, the board is assigned to one of three classification levels.
Classification Level | Max. Abrasion Depth |
---|---|
1 | 0.126″ (3.2mm) |
2 | 0.059″ (1.5mm) |
3 | 0.010″ (0.3mm) |
o Surface Indentation – Measures the ability of a gypsum panel to resist dents caused by small, hard objects by exposing the panel to the impact of a round-tipped rod. Based on the depth of the indentation the impact causes, the board is assigned to one of three classification levels.
Classification Level | Max. Indentation Depth |
---|---|
1 | 0.150″ (3.8mm) |
2 | 0.100″ (2.5mm) |
3 | 0.050″ (1.3mm) |
o Soft-Body Impact – Measures the ability of a gypsum panel to resist a single impact from a heavy soft object by exposing a sample panel to the impact of a swinging leather bag loaded with steel pellets. Based on the energy required to fracture the panel calculated from the leather bag’s weight and drop height, the board is assigned to one of three classification levels.
Classification Level | Min. Fracture Energy |
---|---|
1 | 90 ft·lbf (122 J) |
2 | 195 ft·lbf (265 J) |
3 | 300 ft·lbf (408 J) |
o Hard-Body Impact – Measures the ability of a gypsum panel to resist the impact of a hard object by exposing a sample panel to the impact of a steel cylinder on a pendulum. Based on the amount of force required for the cylinder to penetrate through the panel, the sample is assigned to one of three classification levels.
Classification Level | Min. Penetration Energy |
---|---|
1 | 50 ft·lbf (68 J) |
2 | 100 ft·lbf (136 J) |
3 | 150 ft·lbf (204 J) |
Gypsum panel performance characteristics vary slightly by manufacturer. Consult with the gypsum manufacturer you are considering for the specific classification levels that pertain to your project goals.
Limitations
To deliver the expected wall durability demanded by a multi-tenant residential structure’s design requirements, a number of important limitations should be followed. These recommendations are intended to provide general information only about considerations that are common in this category of special performance gypsum products:
o Abuse-Resistant Gypsum Panels are intended for interior use only
o Abuse-Resistant Gypsum Panels are nonstructural and are not designed to be a fastener base for mounting other materials
o maximum framing spacing should be no greater than 16” (406 mm) o.c.
o avoid exposure to prolonged temperatures exceeding 125°
o do not apply finish to Abuse-Resistant Gypsum Panels before structure is properly closed
o not intended for constant exposure to moisture, ponding or cascading water
o not designed to be used as a substrate for tile applications
Refer to the document GA-216 Application And Finishing Of Gypsum Panel Products for more specific information.
Products vary by brand. For more specific limitations related to the gypsum panel you are considering, consult with the product’s manufacturer.
Frequently Asked Questions
Below are answers to typical questions our technical experts address on a routine basis. These answers may provide additional information you are seeking as well. To submit an inquiry of your own, click here.
1. I’m a little confused. Where should I use abuse-resistant wallboard and where should I use impact-resistant wallboard?
Many designers find that either board will work fine in areas that are subject to a little more “wear and tear.” However, there are some differences to keep in mind when selecting the best board for your application. For example, boards classified as abuse resistant typically have higher abrasion and indentation resistance (meaning a classification level of 2 or 3 per ASTM C1629 for both). Boards that are impact resistant would have similar classification levels for the hard and soft body tests in C1629.
So, is it more likely that the wall could be regularly “side-swiped” by a cart, an individual wielding a suitcase, or someone carelessly carrying a package? Or is it more likely someone might hit the wall “full-on” with a large object as might happen where a hallway terminates into another corridor in a hospital? If the answer is “side-swiped”, you should probably consider abuse resistant boards. If the answer is “full-on,” then you may wish to choose impact resistant to reduce the likelihood of penetration into the wall cavity.
2. How does the installation of abuse-resistant board differ from that of regular wallboard?
Both impact-resistant and abuse-resistant boards have the same basic installation considerations. The latest edition of GA-216 requires that when abuse-resistant and impact-resistant boards are mounted on steel studs, those studs must be .0312″ design thickness (aka 30 mil) or thicker. The reason is that these boards are denser and harder than traditional wallboard. Because more force is needed for screws to penetrate these harder and denser boards, with thinner gauge studs there is a higher likelihood of spinout occurring. Simply stated, the combination of harder board and thinner stud leads to unacceptable rates of spinout and a much lower tolerance for variability in the field, where conditions are never ideal. Aside from this, the taping, finishing, etc. of abuse and impact resistant panels is no different from similar non-resistant counterparts, though it may take a sharper knife and a little more effort to “cut and snap” abuse resistant and impact resistant boards.